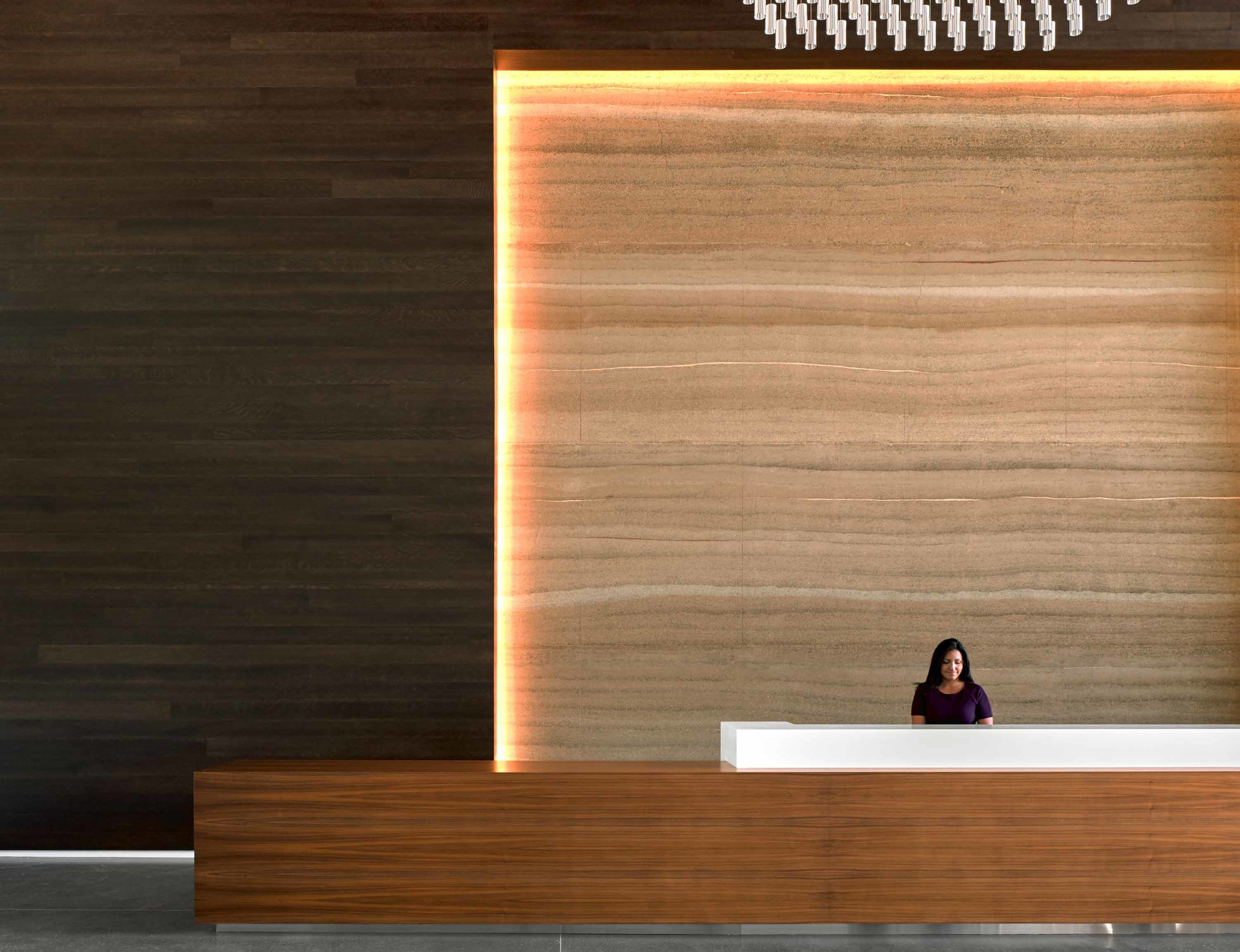
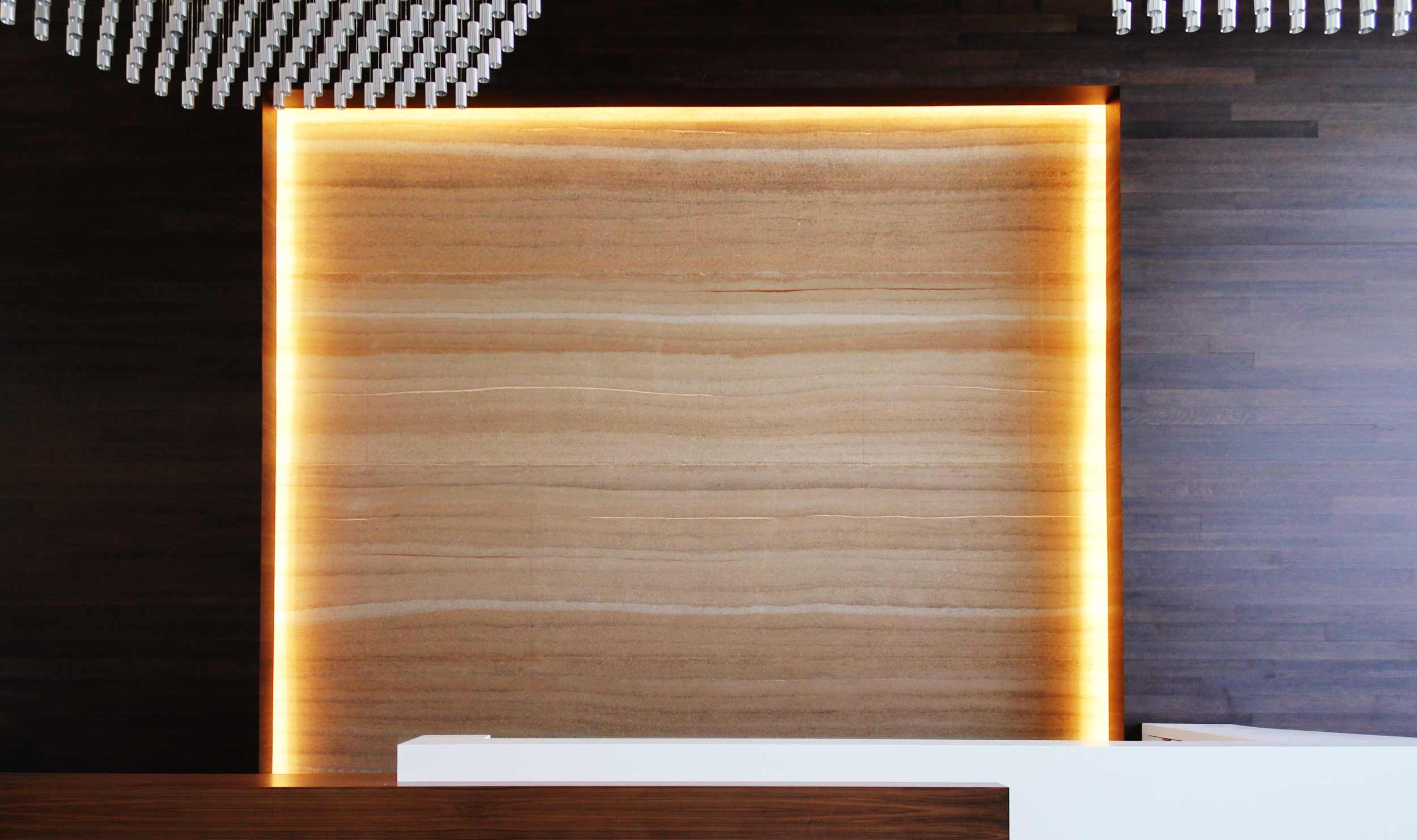

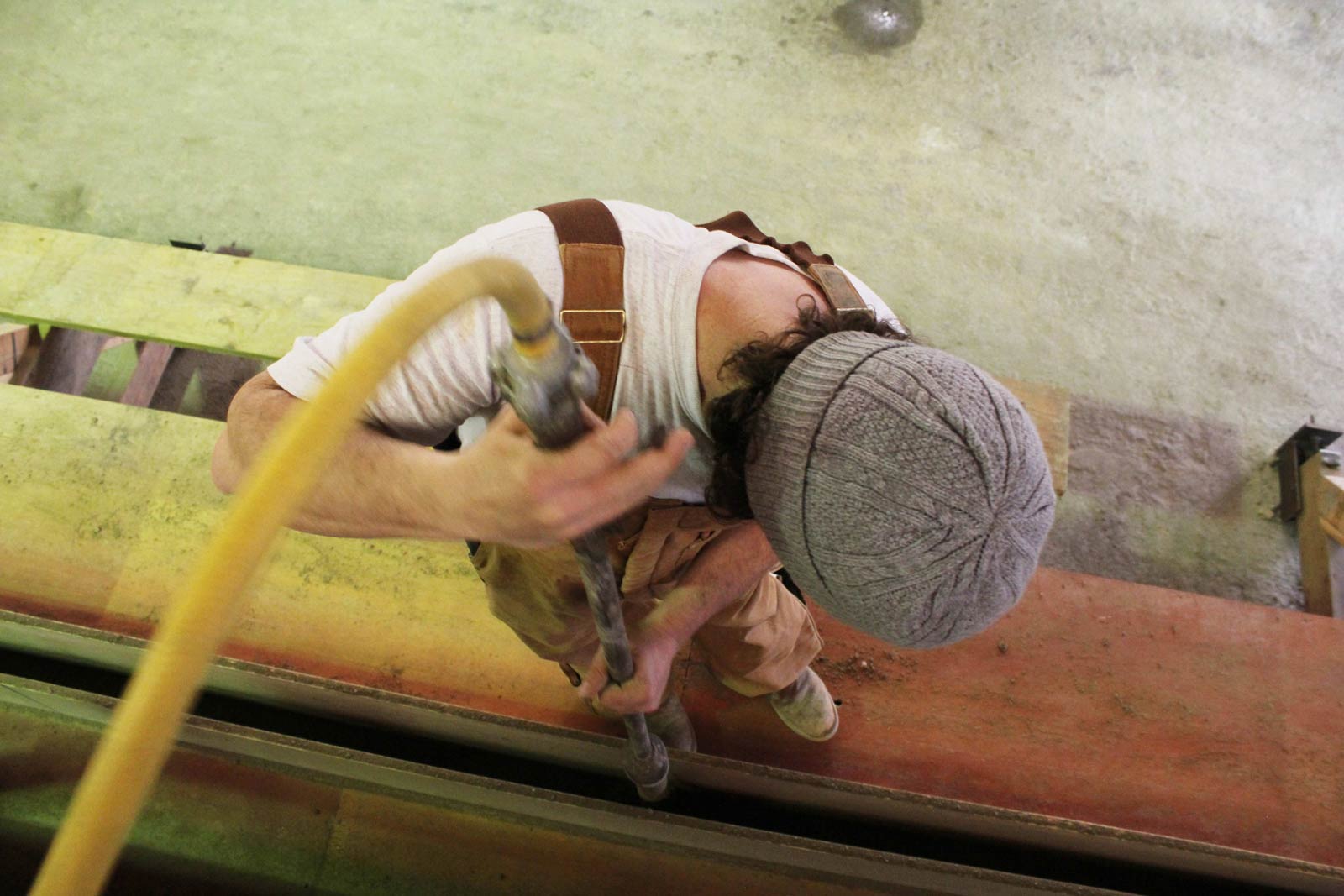
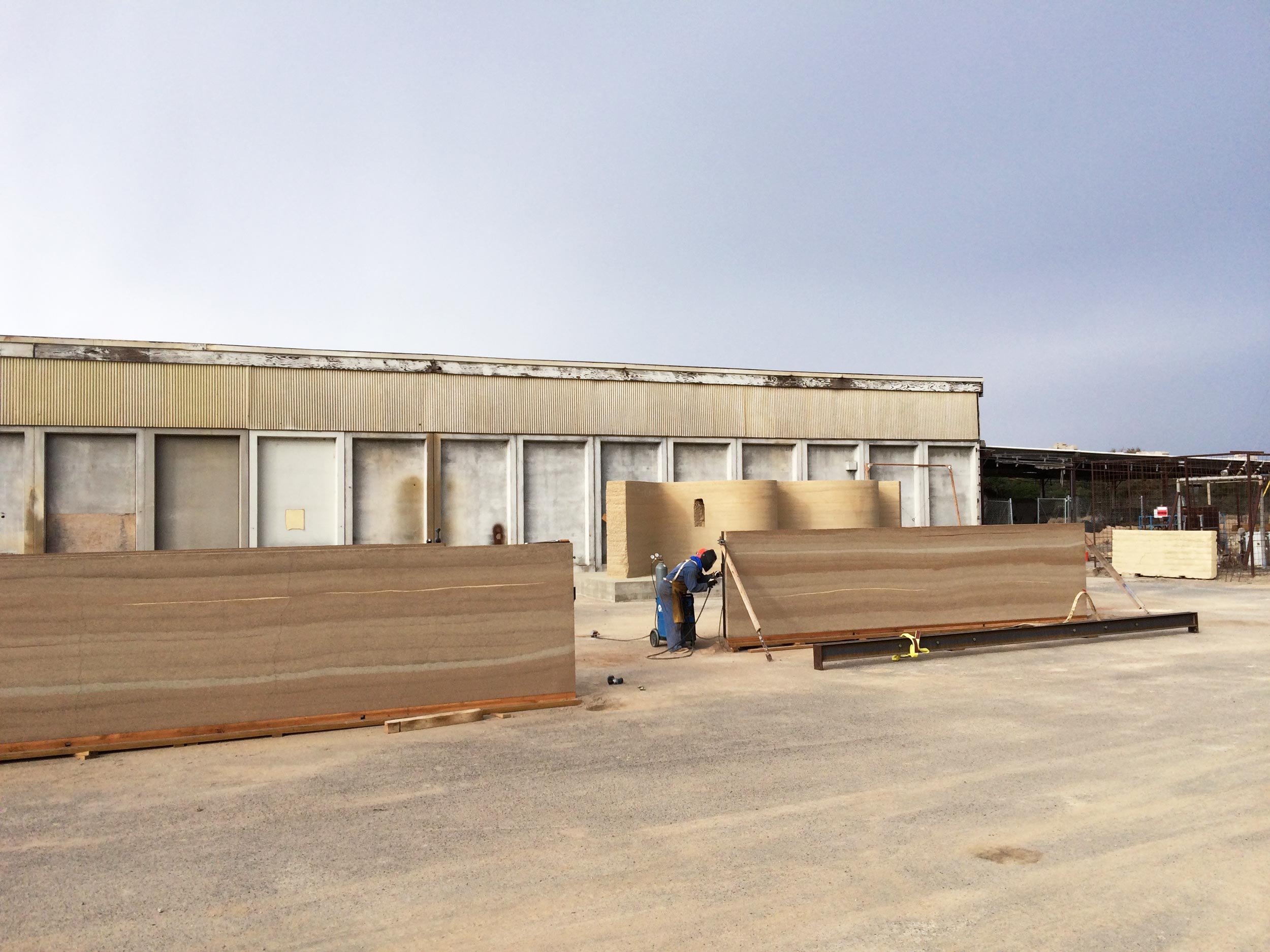
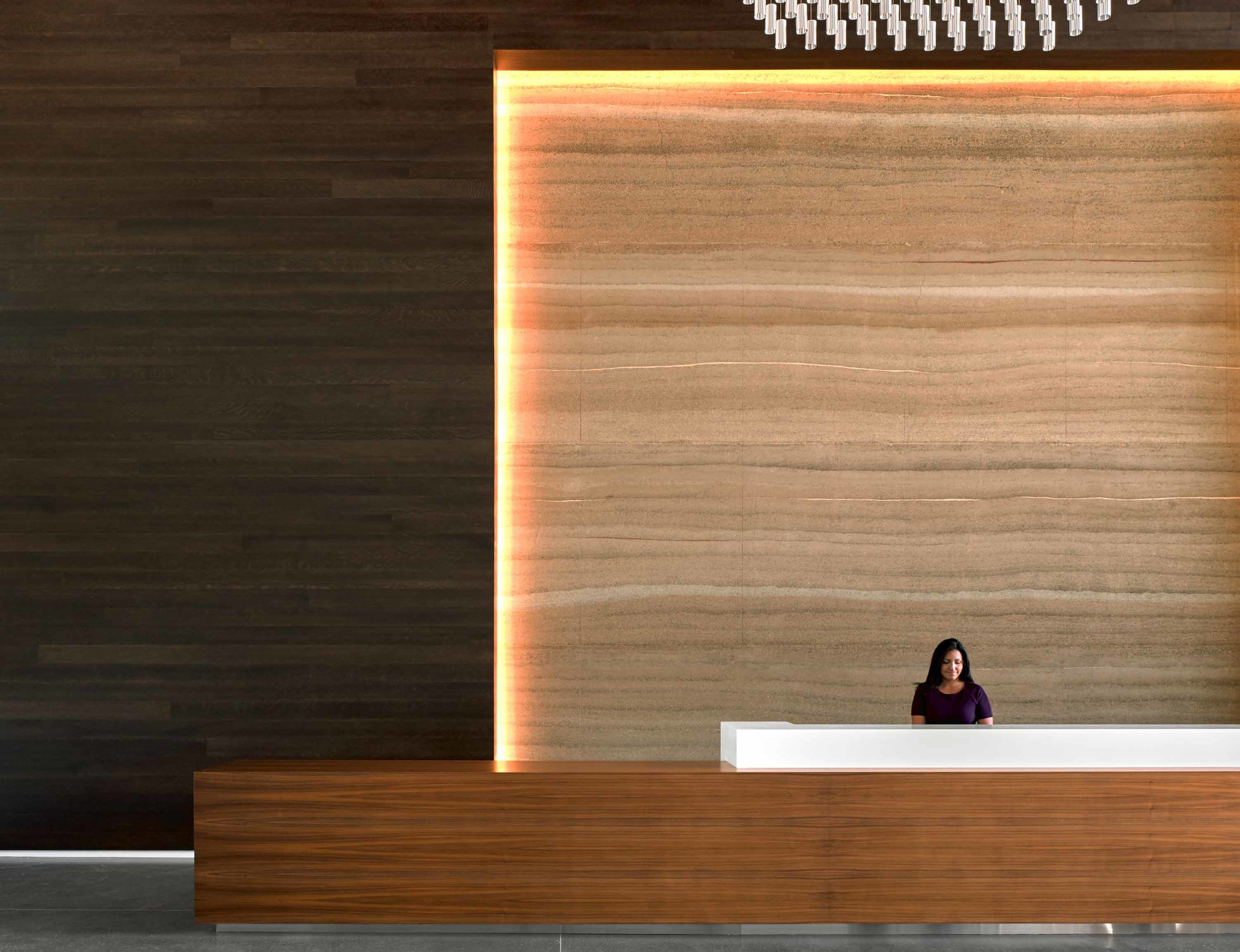
An installation of pre-cast rammed earth panels at the new Stadium Techcenter in Santa Clara, California. Four panels of rammed earth are stacked on top of one another, each panel 5' high and 6” thick, each panel weighed over 8000 lbs. The rammed earth panels were made in our factory in Napa, California and transported to the job site where they were installed on site.
Image © Michael David Rose
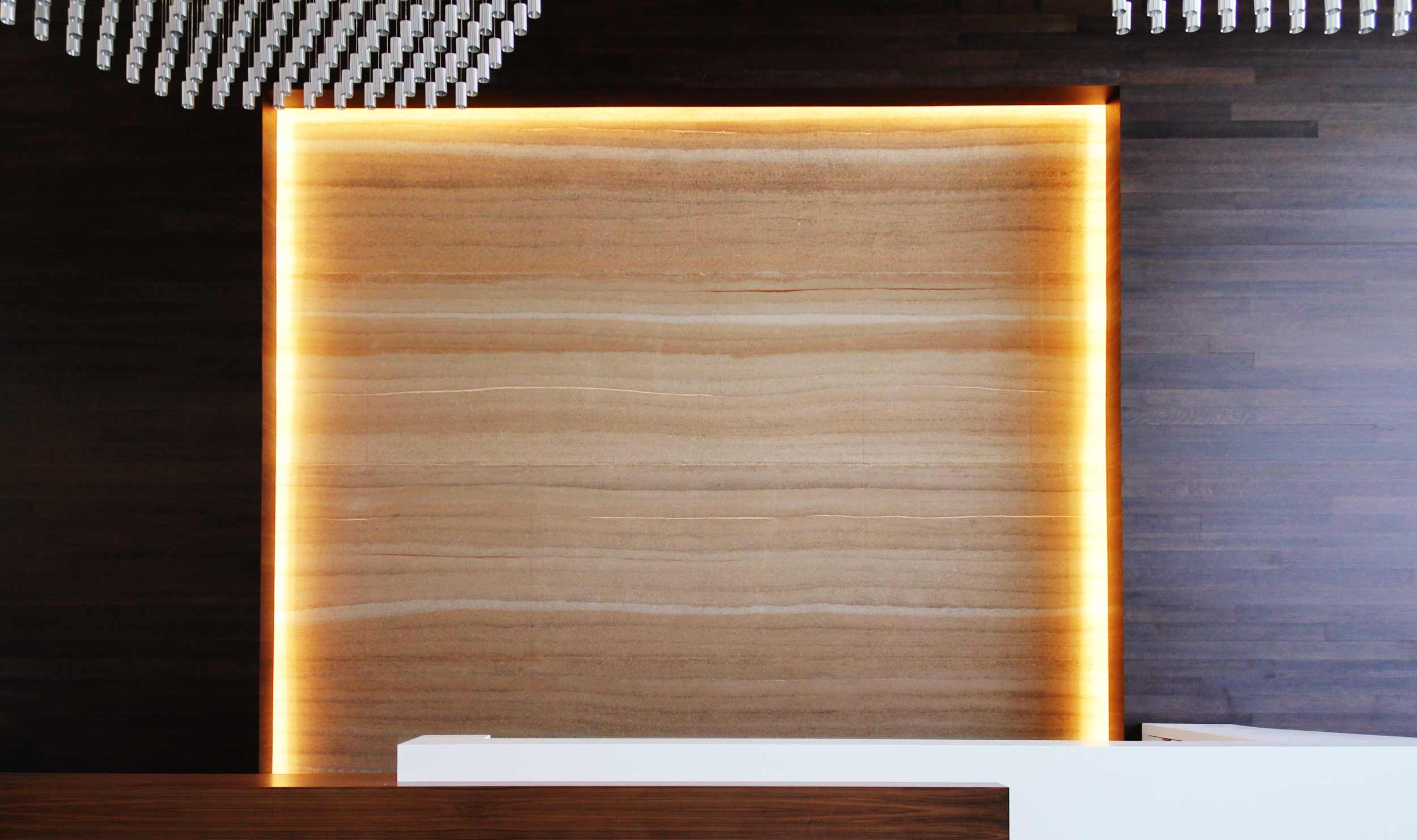
This particular installation could not have been accomplished with traditional methods of monolithic rammed earth in which 18" thick walls are rammed on site - lots of material is needed and large formwork is constructed. In this case, the job site couldn't accommodate the construction of traditional monolithic rammed earth.
The team at Rammed Earth Works has continued to innovate rammed earth technology for 30 years, and the development of pre-cast rammed earth panels is one of the most exciting developments yet. It allows for installation of rammed earth in more applications, and can lead to a lowered cost.

For the installation of the four big Stadium Techcenter panels, we used a long reach forklift to set the panels rather than a crane because the roof was already on the building. The forklift picked each of the five foot high panels off the truck, backed directly into the lobby with only eight inches of space between the door frames and the panels, executed a ninety-degree turn and placed the panels one on top of another against four steel wide flange posts where they were welded in place.
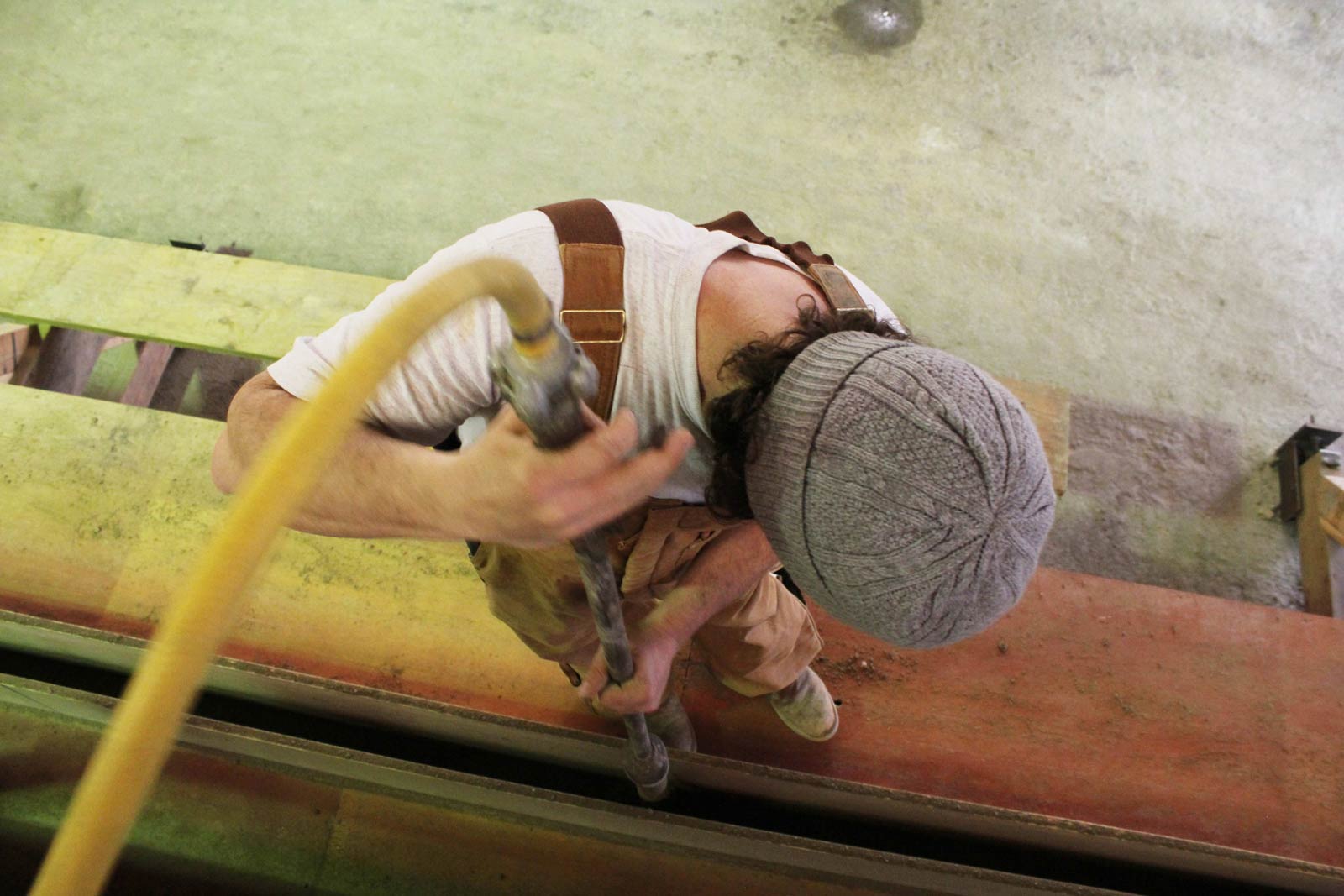
An overhead view of a panels being rammed in the form.
Each five-inch loose lift takes one minute twenty seconds to deposit into the formwork. Target density is 136 pounds per cubic foot. A Jet 2-T rammer has a tool weight of twenty-one pounds, works on 90 psi of air pressure, and has a strike rate of 700 blows per minute. To reach 97% compaction rate, the rammer travels along the twenty-four foot long wall at the same rate as the delivery conveyor - three linear feet every fifteen seconds.